2017
Terraperforma
3D Printed Performative Wall
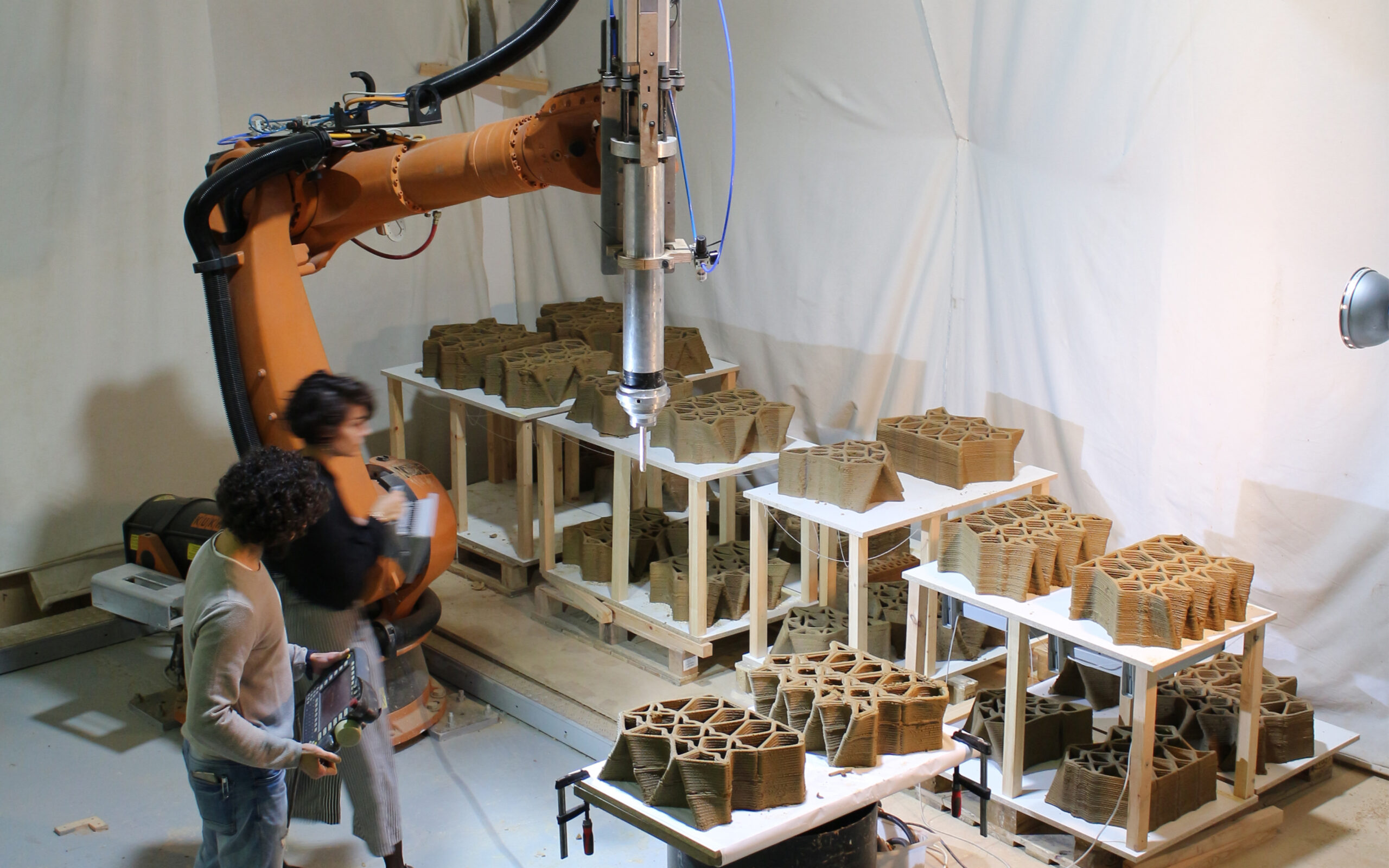
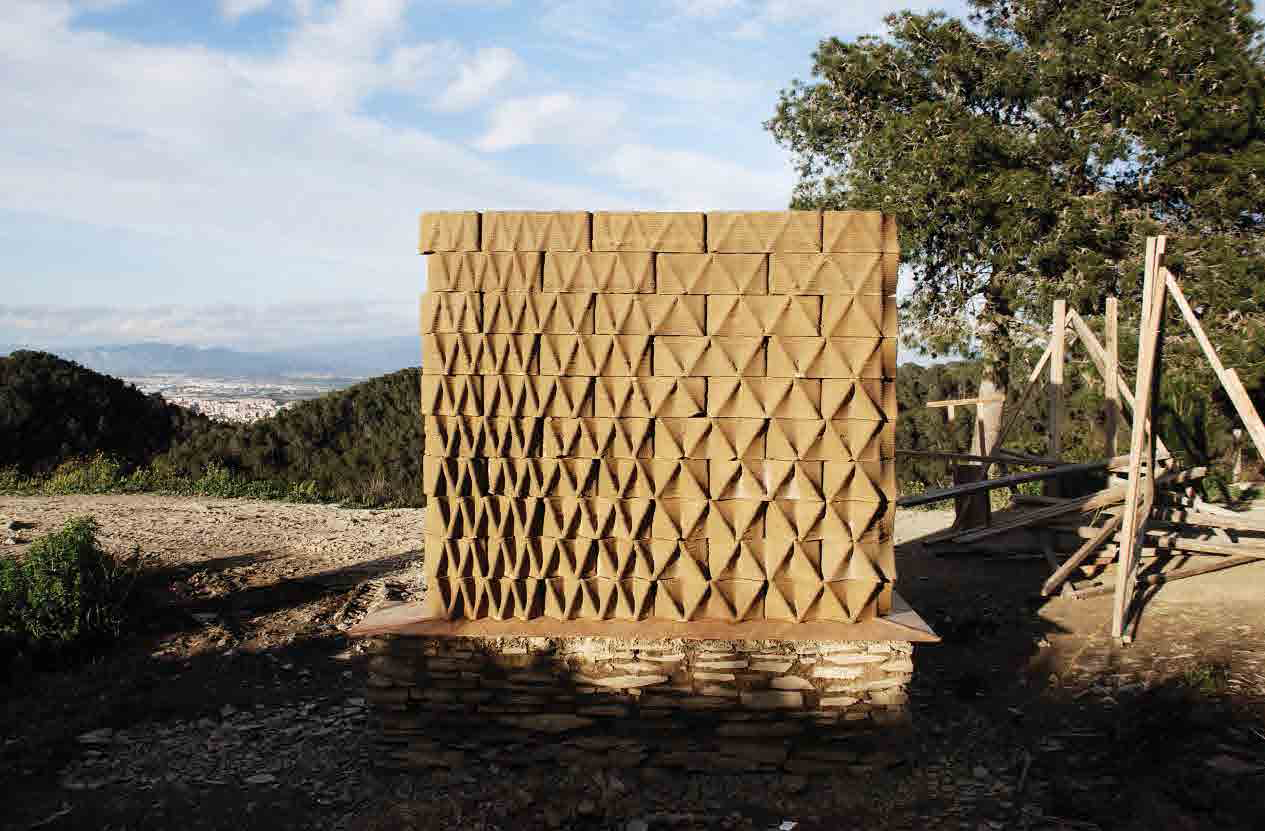
While 3D printing has given the possibility to create complex geometries, the intelligence of the design comes from the optimisation strategies, the creation of performative shapes becoming easier to achieve.
During TerraPerforma, a series of tests were carried out that explore the possibility to optimise the design according to different performance parameters. The development of the project started by researching climatic phenomena and material behaviour. Therefore, a series of physical tests and digital simulations were done for prototypes of walls testing solar radiation, daylight, thermal conductivity, thermal convection, thermal mass and structural behaviour. Software such as Rhino CFD, Ladybug and Karamba were used in order to simulate wind, sun and structural behaviour. The team also developed a series of machines, such as the Hygrothermal Monitoring Apparatus and the Load Machine in order to future develop these studies, as well as doing a light visualisation exercise by recreating the sun path with the help of a robot.
The team also had the opportunity to work within Tecnalia, experimenting with the CoGiro robot, a Cable-Driven Parallel Robot (CDPR) owned by Tecnalia and LIRMM-CNRS Its original point of the design resides in the way the cables are connected to the frame, called the configuration of the CDPR, with makes it a very stable design. Hence the tea was able to manufacture the biggest monolithic piece done within the research.
For the final prototype of TerraPerforma, it was concluded that a modular approach would be best, mainly due to the difficulties of bringing a robot in the outdoor and to face hard climate conditions. The modules are parametrically conceived so that they have optimum performance depending on solar radiation, wind behaviour and structural 3D printing reasoning, both by their own and as a whole design. The facade was conceived as a gradient in both horizontal and vertical directions, having various radiuses of self-shading, in order to optimise the east and west sun.
Additionally, the modules are designed to incorporate various types of openings, in order to maximise the natural daylight potential – the openings are strategically placed and vary from micro openings to full-openings between bricks. The same channels are also designed to aid wind behaviour through convection properties, as well as the placement of the micro-perforation which would direct the air flow.